Wobbler Engine
By Cole Rutkowski
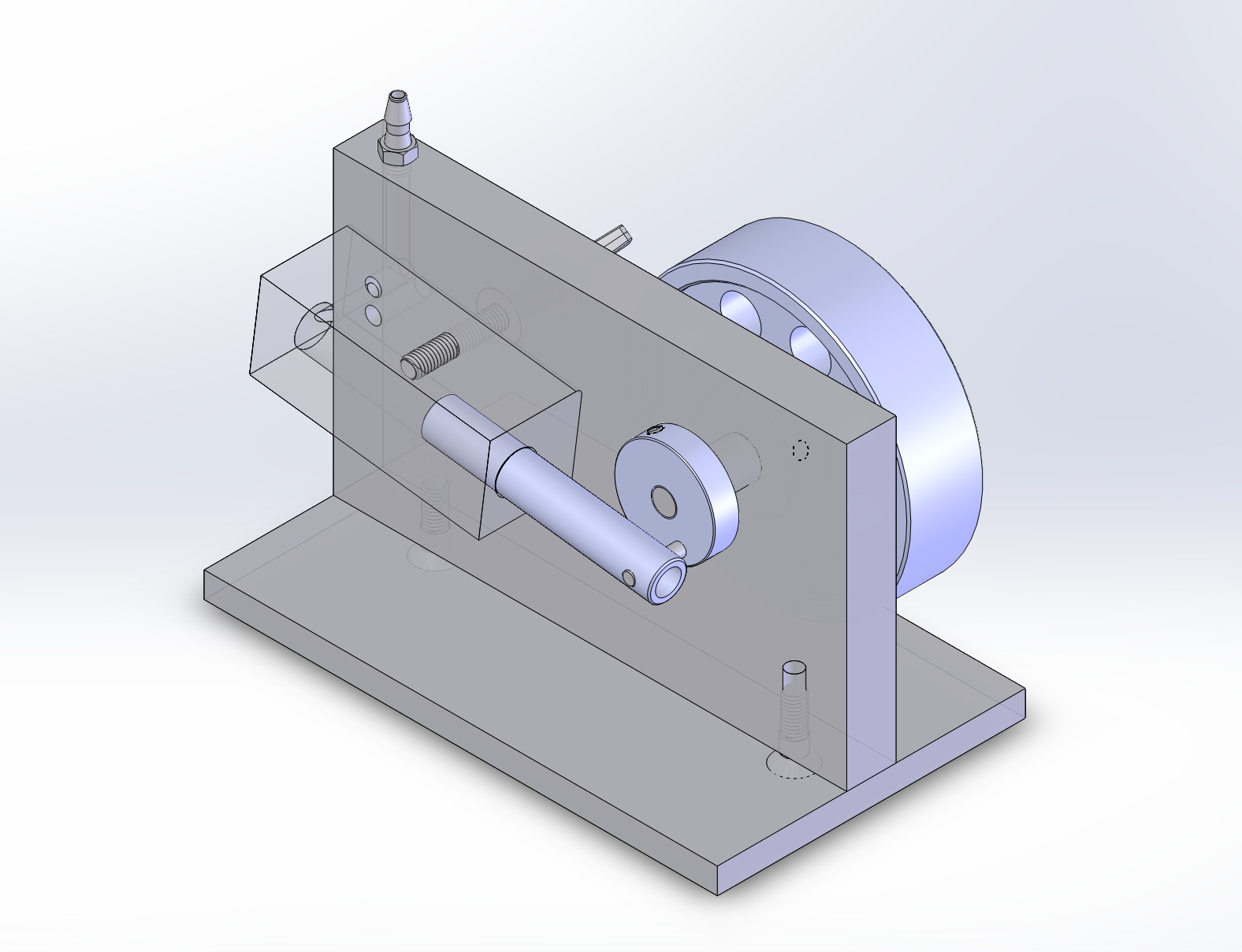
Background:
In the Fall of 2024, I landed a job as a machine shop assistant for MCEN1025, a freshman-level engineering class that introduces CAD modeling, engineering drawings, geometric dimensioning and tolerancing, and manufacturing methods. For their final lab project, students must model an air-powered wobbler engine, create detailed engineering drawings, then manufacture and assemble the parts. The metric each group must achieve is an engine that operates at an air pressure of 10psi or less; the best engines typically run at a pressure of 1-3 psi. On the last day of class, the students compete in an engine runoff and crown a winner for the most efficient engine.
As a shop assistant, I guided the students through the machining of their parts and taught them safe operation of our machines. Most of the students had never stepped foot in a shop, much less seen the machines we used. In the span of five 2-hour timeslots, the students learned how to safely operate our mills, lathes, drill presses, and bandsaws; how to use tools such as chucks, collets, edgefinders, drills, endmills, and reamers; and how read an engineering drawing and determine a sufficient order of operations to manufacture the part.
Having worked with the students all Fall, I was keen on making my own engine. In my spare time, I went in to the shop to make each part again, but this time for myself. Afterwards, I decided to recreate the models and drawings based off of my knowledge and memory of the drawings the students used in the shop.

Assembly
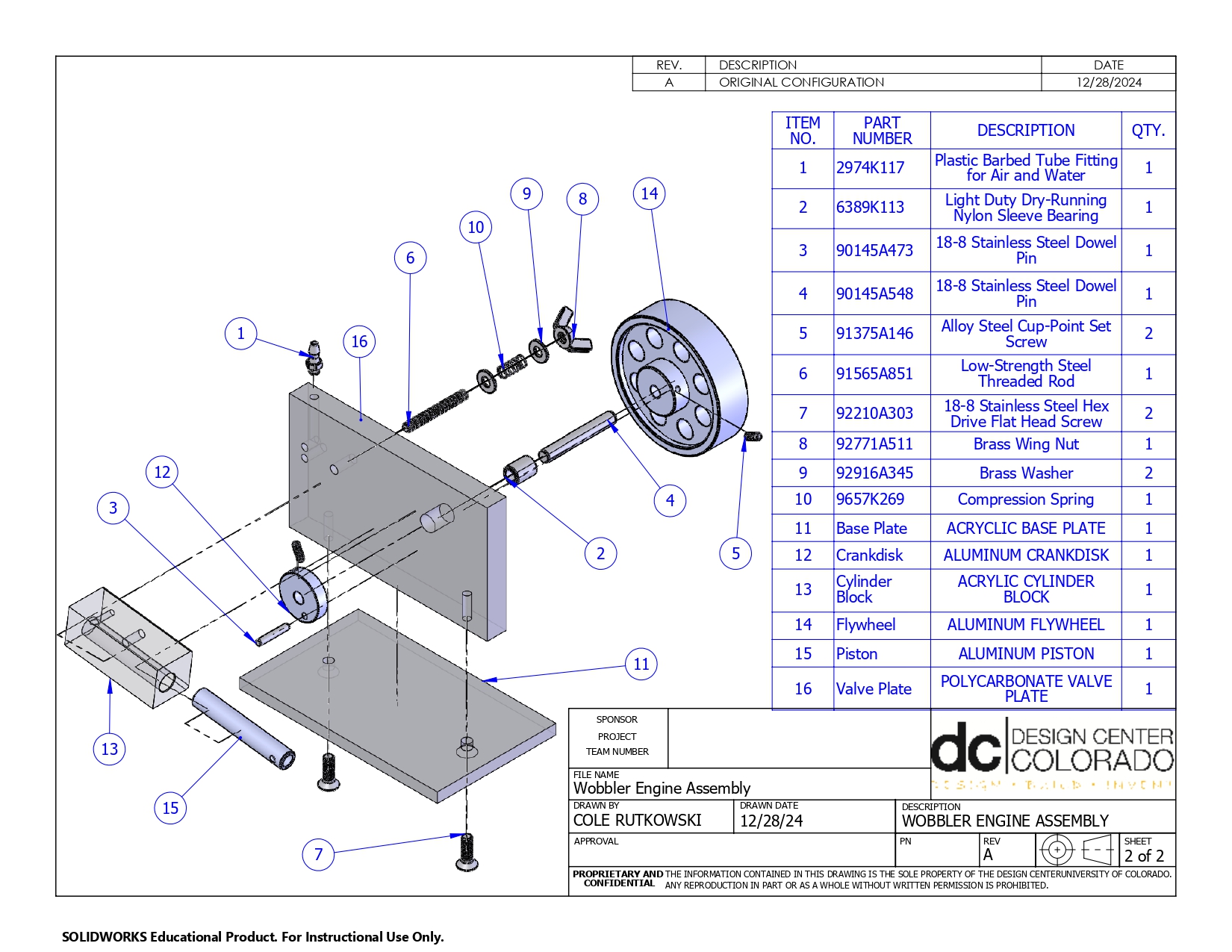
Exploded Assembly
Results:
After manufacturing and assembling my engine, I was ready to put it to the test, head-to-head with the students I worked with all semester. On the day of the runoff, I was able to compete in a special student-vs-assistant competition after the student winners were crowned. In my race, I was put up against the 5 best engines, ultimately finishing the run-off in 2nd, behind the overall winner of the student competition. Out of 100 students, I was very happy to place 2nd and even more impressed with the quality of the winning team. The top 5 groups all ran at 3 psi, and I was able to hit 2 psi before sputtering out, but the winning engine was still chugging along at 1 psi!
My role as a shop assistant helped me expand my shop knowlege and machining skills. The repitition of making parts for students made me more efficient with lathes, mills, and reading engineering drawings. Teaching strengthed my confidence and gave me a stronger understanding of machining. I also refreshed my CAD skills by revisiting the design part of the project. I am incredibly grateful to have worked with knowledgable machinists and fantastic students throughout the semester. Above, you can find the drawings and model of the engine.
My Engine
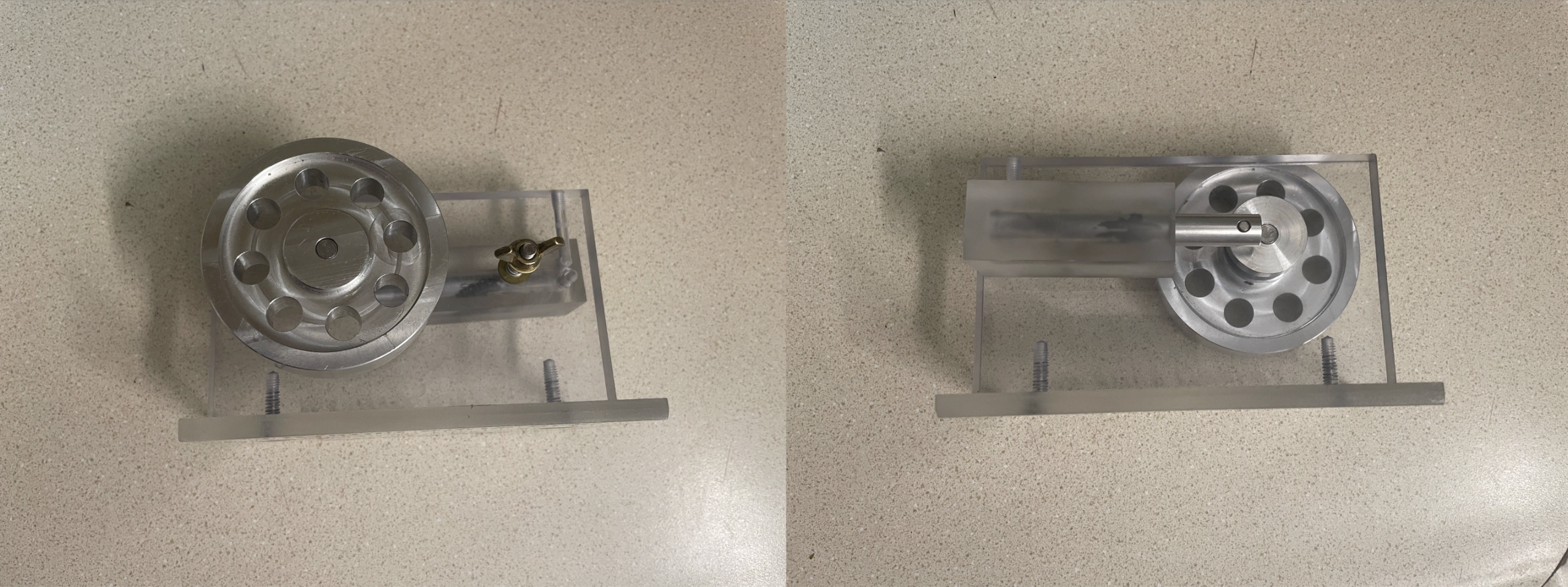